VinFast Car’s state-of-the-art paint technology
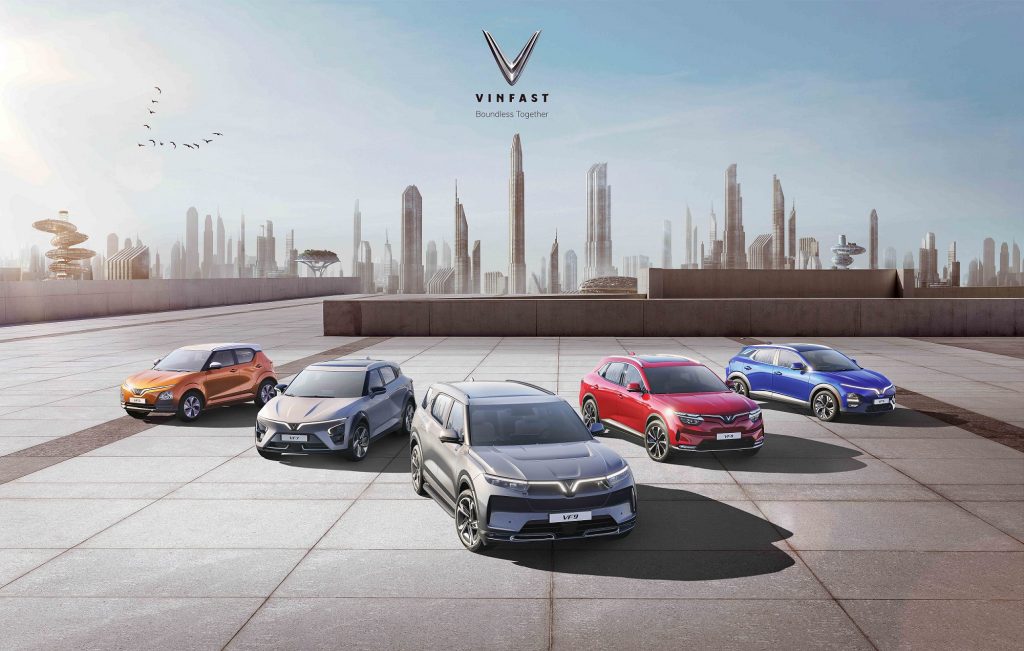
How has VinFast invested its money to ensure that its vehicles have paint that is of high quality, long-lasting, and aesthetically pleasing? The answers to this question can be found in this article.
1. Automotive paint technology
1.1. What exactly is automotive paint technology, and what methods are included in it?
The term “automotive paint technology” refers to the technology that is used to paint automobiles, either on assembly lines for new vehicles or in auto repair shops. Over the course of its history, automotive paint technology has seen significant advancements that have resulted in a rise in the rate of automation to over 100%, as well as cost and time savings.
Today, there are three widely used approaches to painting automobiles:
- Spraying: Spraying is the most frequently used method for applying automotive paint, and it is utilized by a variety of businesses, including auto repair shops and automobile manufacturers. Spraying is an extremely flexible and cost-effective approach for applying a coating; it saves both time and money. Spraying is also the most straightforward way to ensure that the paint quality is consistent throughout a job.
- Dipping: This requires an entire component to be submerged in a paint bucket, meaning this technique is often reserved for use by automobile manufacturers or large-scale repair shops. The full automotive paint line also makes use of a procedure known as dip coating.
- Brushing: As it must be carried out by hand, this technique of painting is among the least utilized and is typically reserved for the application of paint to minute details, or for the process of hand-painting supercars with intricate detailing.
1.2. What kind of paint technology is the highest caliber?
Paint technology is of the highest caliber when it meets the following issues:
- The car’s paint quality is consistent and long-lasting despite the passage of time.
- The car painting line is operated and managed completely automatically.
- The paint business is risk-free as it employs procedures and supplies that lessen the negative impact on the surrounding environment.
- The car paint line functions in such a way that it saves time, money, and fuel.
Currently, the most advanced paint technology used by most car manufacturers is Electrolytic Dipping Coating, also known as ED Coating.
1.3. Standard automotive paint process according to Electrolytic Dipping Coating
The process of Electrolytic Dipping Coating includes the following main stages: Pretreatment – Electrodeposition (ED) Coating – ED Drying – Polishing – Sealant, PVC Spray – Primer – Primer Oven – Top Coat – Top Oven – Inspection.
- Pretreatment: During this stage, the bodywork goes into the paint line and must pass through the washing tanks in the following sequence: degreasing tank, industrial water tank, activation tank, phosphate tank, and DI water tank. The procedure of dipping the automobile body in the tank is accompanied by nozzle cleaning that removes any impurities, dirt, and prepares the surface for the application of the ED coating.
- Electrodeposition (ED) Coating: After undergoing pretreatment, the bodywork undergoes ED Coating. During this step of the process, the body of the vehicle is submerged in the paint tank to produce a film utilizing cathodic electrodeposition. After being removed from the tank, the vehicle’s body undergoes a series of additional processes that involve being dipped into the UF and DI tanks. After the completion of this step, the body of the vehicle is covered in a layer of paint that is resistant to oxidation. Thanks to cathodic electrodeposition, the thickness of the paint film is consistent.
- ED Drying: The next step involves passing the bodywork through a heating chamber. In this section of the furnace, the vehicle’s body is moved through two preheating chambers as well as the primary drying chamber. A cooling system is located at the end of the chamber to assist in bringing the body temperature down to an appropriate level before moving on to the next step.
Polishing, PVC Spray for Car Underbody, Sealant Spray: Sanding machines are used at this stage to polish any paint areas that are less than ideal. Then, the body of the vehicle is transferred to the area designated for gluing, where it is sprayed with PVC and sealed before moving on to the next step. - Primer: At this stage, the bodywork is covered with a primer.
- Primer Oven: After the application of the primer is finished, the vehicle’s body is dried once again so that the paint can set more quickly.
- Top Coat: The car body is then transferred to the paint chamber, which is also referred to as the top coat. At this point, the colors that will be available to customers in the next step are painted onto the bodywork. After the application of the colored paint comes the clear coat, which helps protect the underlying layers of paint.
- Top Oven: After the body of the car has been painted, it is given time to dry once more.
- Inspection: An inspection chamber is used on the body of the vehicle before it is transported to the assembly facility. This is done to guarantee that the paint quality is consistent throughout the vehicle and that there are no faults. If an error is found, the chassis of the vehicle will be moved to the area designated for repairs.
Robotic arms and conveyor systems are typically utilized to achieve full automation throughout the whole Electrolytic Dipping Coating process. The coating process for a car body typically takes between 14 and 18 hours, with the average time falling somewhere in the middle.
The culmination of this complete coating process results in a layer of paint that has a number of distinct layers; nonetheless, the overall thickness is only about the width of a single human hair.
2. Paint technologies applied to VinFast cars
At VinFast, cutting-edge paint technology is used on all the company’s models, ranging from the VinFast Lux A2.0 and LUX SA2.0 to recently introduced electric car models like the VinFast VF e34 and VinFast VF 8. The paint shop is run nearly entirely by robots to produce cars with a long-lasting, high-quality paint coverage in a variety of colors .
High-class paint technologies applied by VinFast in its paint shop include:
- Brand new EcoPaint robot: The car paint shop that VinFast maintains is outfitted with the most recent generation of completely autonomous EcoPaint robots. These paint robots have a seven-axis mechanical arm that does not require rails, which allows them to be incredibly nimble. As a result, a significant amount of space and investment expenditures are saved. In addition , the robot is fitted with sensors that can supply data for investigation and evaluation in real time.
- EcoInCure: EcoInCure ensures rapid drying of the paint while maintaining a high degree of paint quality by utilizing an inside-out heating method and optimizing airflow.
- Improved RoDip coating technology: Throughout the entirety of the pre-treatment and ED Coating stages, the enhanced RoDip dipping technique with its significantly increased productivity is utilized. As a result of the rotational motion, the body of the vehicle does not have to tilt into and out of the tank as frequently as it did previously, which helps to bring the overall size of the tank down. This results in cost savings due to the decreased consumption of energy, water, and chemicals.
- EcoDry X Dry Separation: EcoDry X is a filtration system that is comprised of multiple stages and is used to separate leftover spray dried paint. It is constructed out of filter carts, each of which has six filter cartridges, as well as a bottom bag filter that acts as the system’s second stage of filtration.
- Industrial Internet of Things (IIoT) technology: All robots and machines in the paint shop are fitted with sensors that can collect data in real time for monitoring and analysis.
3. Paint shop at the VinFast factory
VinFast has an odorless, state-of-the-art paint shop that ranks first in Vietnam in terms of automation, all in an effort to fulfill the market’s demand for a large quantity of automobiles to be sent there. The paint shop at VinFast was constructed by Dürr, a multinational corporation that specializes in manufacturing and mechanical engineering and is currently the world’s leading paint shop implementation partner.
VinFast’s paint shop at its factory in Hai Phong is 20,000 square meters in size and is run nearly entirely by robots and automatic control lines that were brought from Europe. The paint shop has an automation rate of 95%. As a direct consequence of this, the quality of the automotive paint produced by VinFast is checked and double-checked to ensure that there are no mistakes.
The paint shop has an automation rate of 95%
VinFast automobiles have the highest possible paint quality and durability thanks, in part, to the RoDip electrostatic power coating system. This is the latest generation of robot and features an air circulation system in the paint chamber that is designed in accordance with sophisticated dry filtration technology. Following the painting process, the vehicle is moved to a storage area that has individual cells. This is done to prevent the paint from becoming contaminated with other colors, dust, or other unnatural substances.
VinFast’s car paint quality is 100% controlled thanks to automatic control lines imported from Europe.
In addition, VinFast is an industry trailblazer when it comes to giving clients a wide range of paint color options to choose from. Clients are given the opportunity to freely express their own unique personalities, and the vast array of paint color possibilities ensures that VinFast automobiles always have the most trendy hues.
Both VinFast VF 8 and VF 9 have attractive exterior colors such as VinFast Blue, Sunset Orange, Crimson Red, Brahminy White, Desat Silver, Neptune Gray, Deep Ocean, and Jet Black.
Bạn cần đăng nhập để tương tác với nội dung này: Đăng nhập.